一つ戻る。ページをめくり没入。
エクスクルーシブ、ユニーク、インスピレーションたっぷり。クリストフォーラスは、ポルシェ愛好家のための雑誌です。その歴史はポルシェそのものと同じくらい長いものです。1952年の発刊以来、ポルシェという企業、そしてこの企業を形作ってきた人々、製品、歴史、モータースポーツなど、様々なストーリーをとりあげながら読者を魅了し続けています。
紙媒体によるポルシェマガジンは、世界中で毎年4回、毎号約60万部、10の言語で刊行されています。クリストフォーラスは、世界有数のカンパニーマガジンとみなされており、バックナンバーはコレクターアイテムとしても愛され続けています。
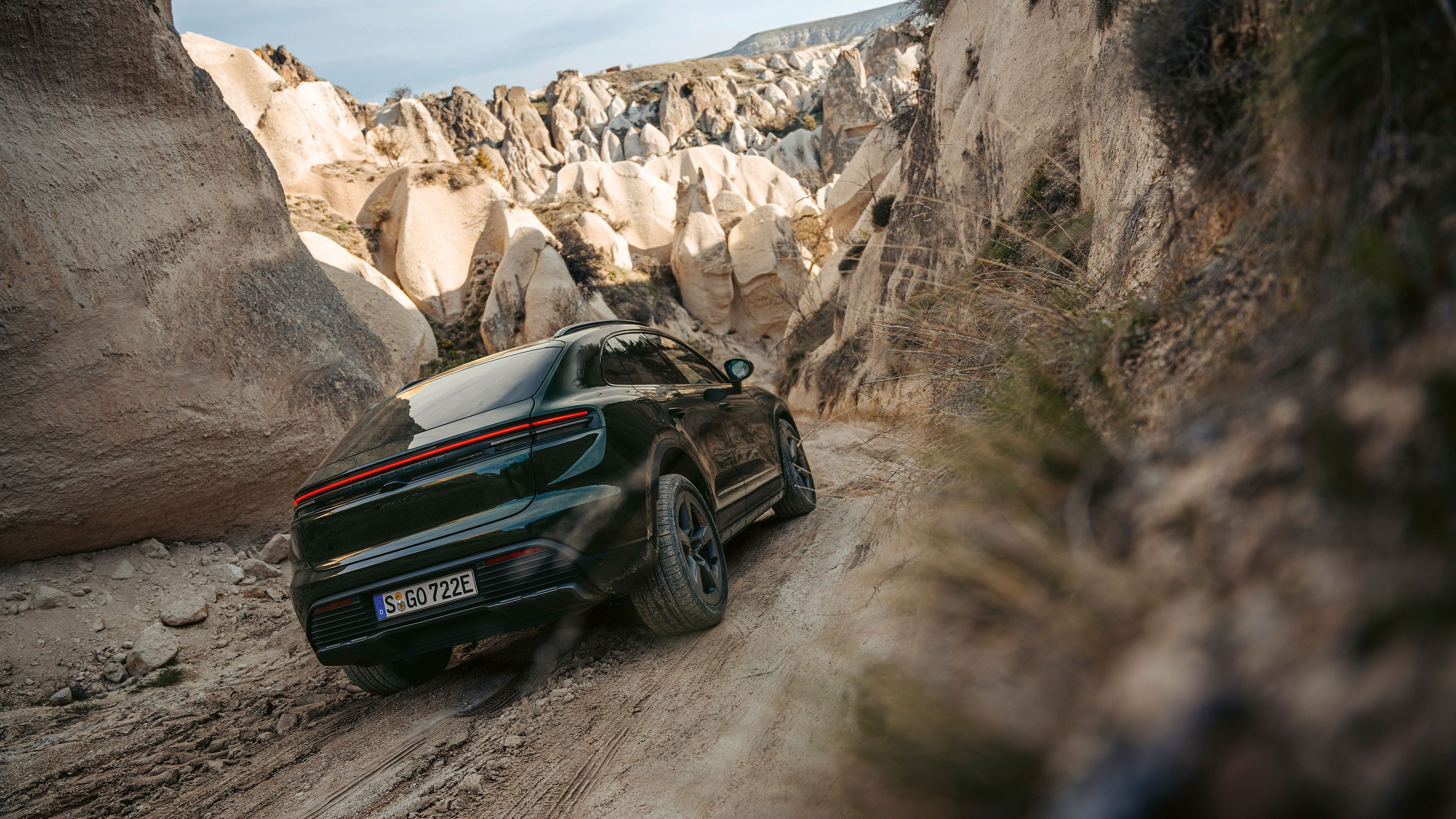
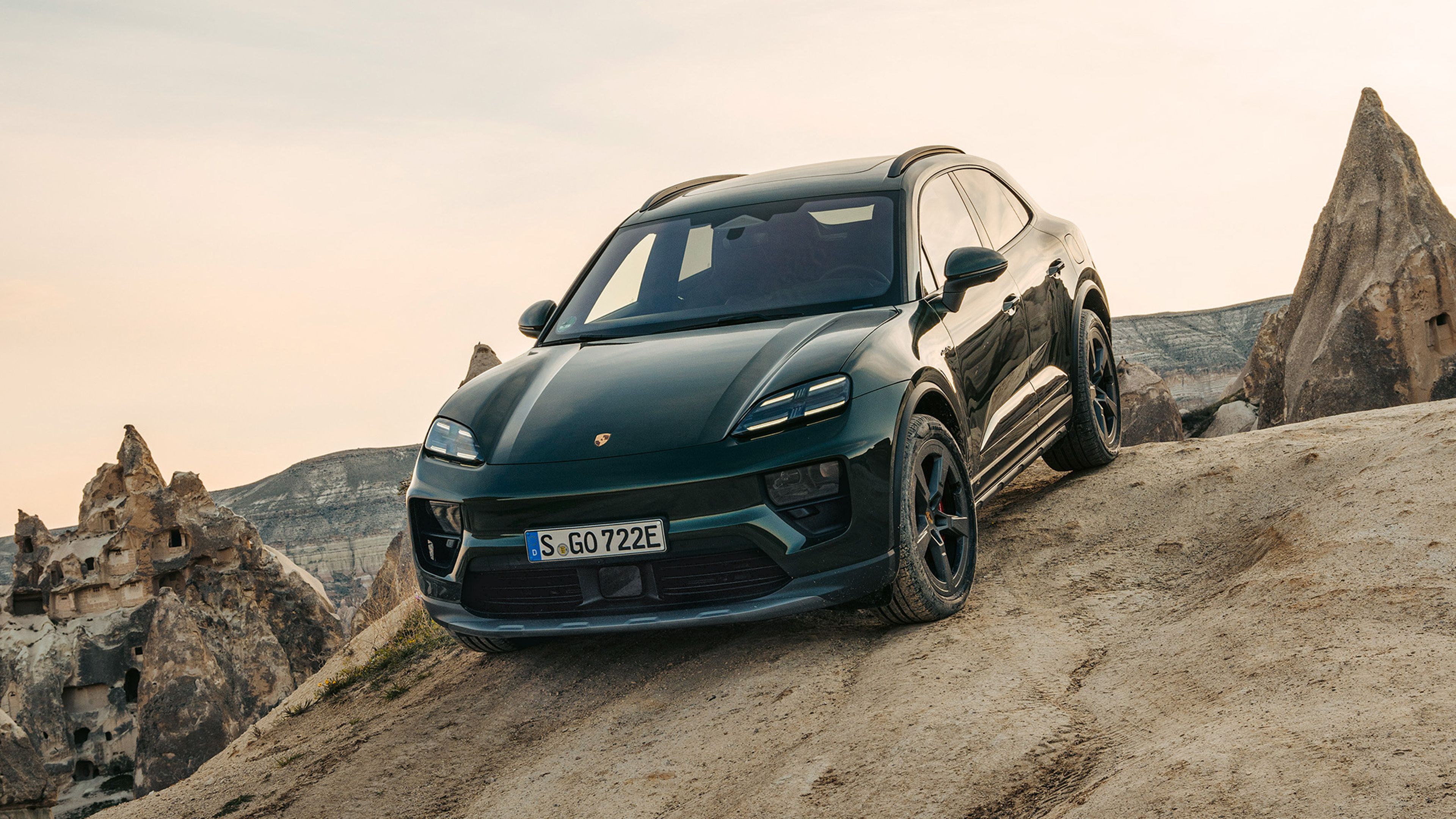

Nº415
アスファルトから離れて
いびつな岩壁、色とりどりの熱気球、古代の洞窟、そして、美食。カッパドキアは印象的な舞台装置を提供する。 つまり、新型マカン4Sのような場所だ。 クリストフォーラスがこのクルマで、トルコで今人気急上昇のこのエリアを探検した。それも大半はオフロードモードで。

定期購読のお申し込み
季刊クリストフォーラスを24ユーロで定期購読。