Scalare una marcia. Sfogliare. Perdersi.
Esclusivo, straordinario, suggestivo: Christophorus è la rivista per gli appassionati di Porsche. E ha quasi la stessa età del brand di auto sportive: sin dalla sua prima edizione, uscita nel 1952, la pubblicazione entusiasma i suoi lettori con racconti incentrati su Porsche, che vedono protagonisti personaggi famosi, prodotti, storia e Motorsport.
La versione cartacea del Porsche Magazin viene pubblicata in tutto il mondo quattro volte all’anno in 10 lingue, con una tiratura di circa 600.000 esemplari per numero. Christophorus è una delle riviste aziendali più rinomate al mondo. Gli esemplari storici sono molto ambiti dai collezionisti.
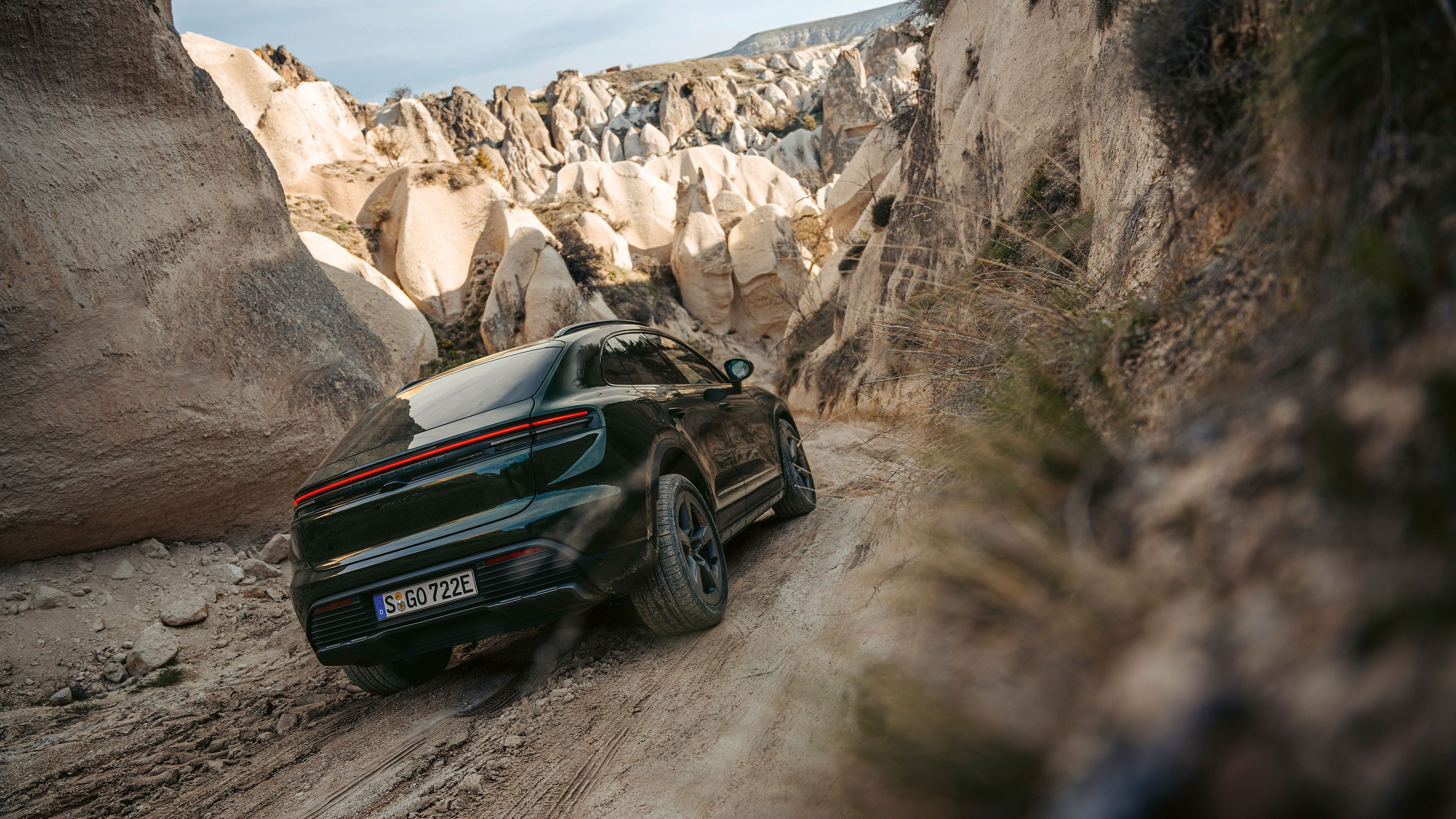
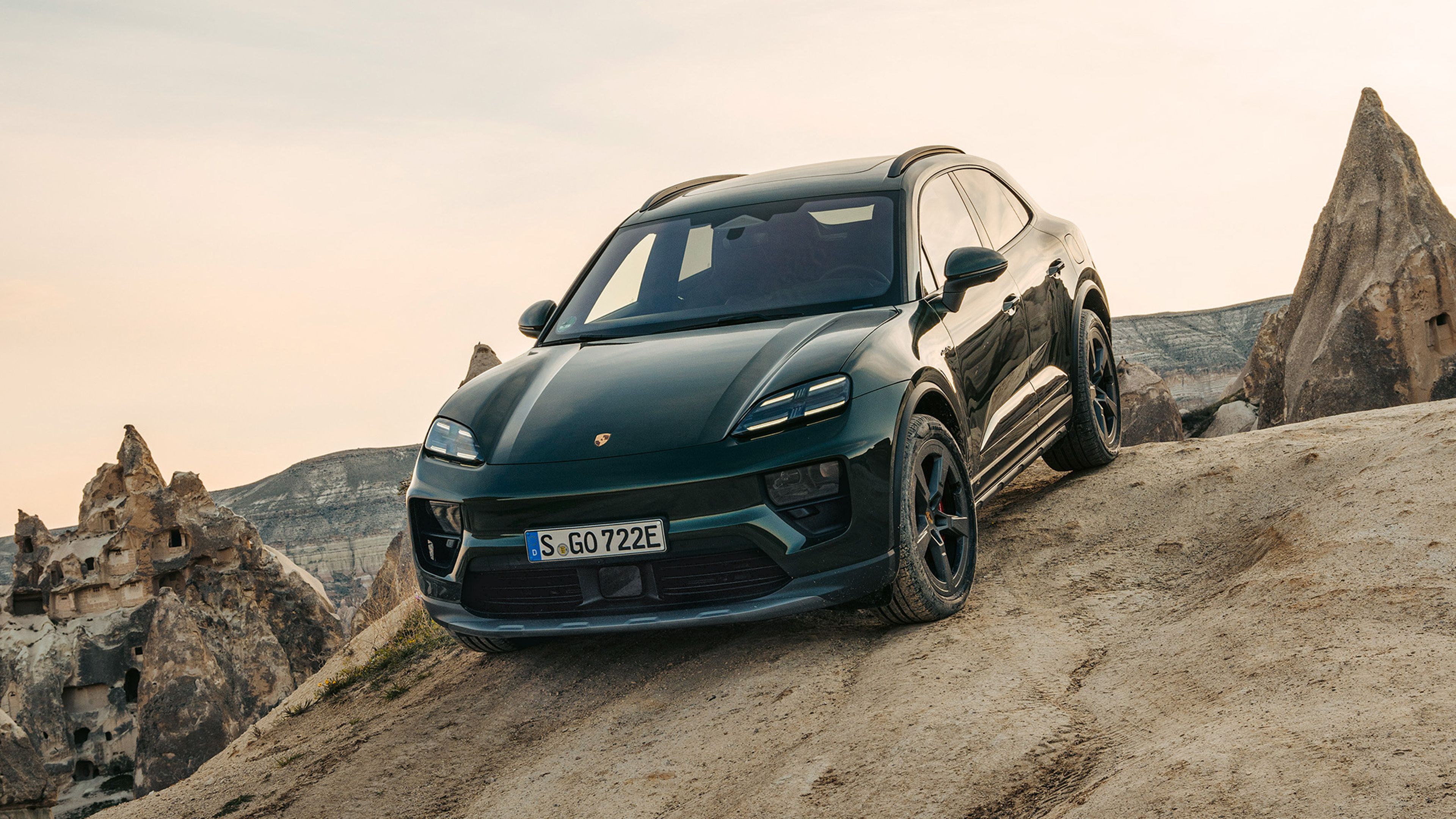

N° 415
Lontano dall’asfalto
Rocce bizzarre, mongolfiere colorate, grotte antichissime e prelibatezze culinarie: la Cappadocia offre una cornice incredibile. Analogamente alla nuova Macan 4S, con la quale Christophorus esplora la popolare regione della Turchia. Per lo più in modalità offroad.

Abbonarsi
Ogni anno vengono pubblicati quattro numeri di Christophorus, disponibili in abbonamento al costo di 24 euro.